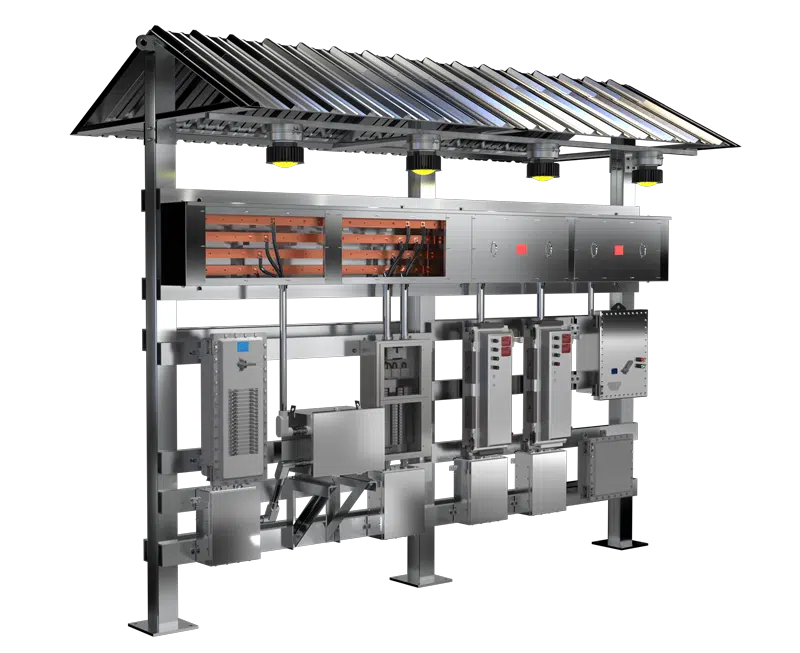
In the petrochemical and heavy industrial sectors, the method of electrical distribution significantly influences a project’s safety, reliability, and overall financial outcome. The two leading methods, switchracks and substations (both modular and traditional site-built), offer distinct advantages and disadvantages. Understanding these differences is essential for engineers, EPCs, and end-users aiming to select the most cost-effective and safe solution for hazardous location (HazLoc) environments.
Defining the Options
Before we dive into specifics, let’s define clearly what a switchrack and substation entail:
- Switchrack: A pre-engineered, free-standing metal structure assembly that includes circuit breakers, motor starters, panelboards, transformers, and other control equipment, designed specifically for hazardous areas.
- Substation: Usually consists of modular buildings or traditional concrete block structures that house similar electrical equipment but require additional field installation and coordination, typically situated in non-hazardous or less hazardous areas.
Both have their place, but let’s unpack the critical differences impacting cost, site utilization, and safety.
Project Timeline and Cost Savings
One of the primary advantages switchracks provide over substations is the dramatic reduction in project timelines. A switchrack can move from design approval to full commissioning within approximately three to six months. In comparison, modular substations typically require six to ten months, and traditional concrete substations can extend to twelve to twenty-four months. The reason behind this substantial time reduction lies in the standardized, pre-engineered nature of switchracks.
Switchracks are assembled entirely off-site and undergo thorough testing before shipment. This factory-driven approach substantially reduces the complexity and risk of field installation. In contrast, conventional substations involve extensive onsite construction, including detailed project scheduling, multiple vendor coordination, and extensive field labor for installation and commissioning. This inherent complexity introduces project risk, delays, and cost overruns.
Minimizing Environmental and Space Impact
Switchracks offer significant environmental and space benefits compared to substations. Traditionally, substations are located outside hazardous zones to mitigate explosion risks, meaning they require substantial additional real estate—often up to 8,000 square feet when accounting for required buffer zones. Conversely, switchracks designed explicitly for hazardous environments can be safely installed within classified areas, needing as little as 200 square feet.
For expanding or congested petrochemical facilities, this advantage is substantial. Switchracks eliminate the necessity of costly purging or pressurization equipment typically required for substations placed near or within classified zones. Additionally, because they can safely reside within hazardous areas, switchracks remain compliant even as facilities evolve, and hazardous area boundaries shift due to process expansions or modifications.
Safety and Compliance
Safety is an overriding priority in hazardous locations. Switchracks are meticulously engineered to IEEE and UL specifications, ensuring that structural integrity, electrical safety, and environmental resistance are prioritized. Unlike many substations, where field installation variances can introduce safety risks, pre-engineered switchracks are consistently constructed and rigorously tested under controlled factory conditions.
Key safety benefits of switchracks include:
- Built-in Compliance: Switchracks comply with all applicable standards and codes, including area classification (Class I, Div 1 & Div 2), grounding requirements, and arc flash protection.
- Enhanced Reliability: Comprehensive factory testing significantly reduces the potential for faults and failures upon startup, reducing personnel risk and operational downtime.
- Simplified Maintenance: Switchrack designs provide easier access for routine inspections, infrared thermal imaging, and preventive maintenance, significantly enhancing safety and reliability throughout the equipment’s lifecycle.
Economic Advantages: A Detailed Look
The economic benefits of switchracks extend beyond initial capital expenditure. The reduced installation complexity directly translates into lower labor and commissioning costs. Additionally, switchracks require significantly fewer engineering resources for procurement, coordination, and scheduling compared to conventional substation projects.
Financial analyses consistently show that switchrack installations can save roughly 50% in overall costs compared to equivalent modular or traditional substations. These savings come not just from initial expenditures but also through substantial ongoing operational efficiencies, reduced downtime, and minimized long-term maintenance needs.
Flexibility and Expansion Capability
Another critical advantage of switchracks is their built-in flexibility. Switchrack designs inherently support future expansions or modifications with minimal additional infrastructure. This capability contrasts sharply with substations, where expansion typically requires significant construction, infrastructure modification, and associated high costs.
Switchracks feature multiple open sides for easy addition of new equipment or loads, facilitating future growth without major site disruption. Such flexibility also enhances disaster resilience, as switchracks can be physically separated, preventing single points of failure common in centralized substation configurations.
Installation and Maintenance Simplicity
Installation simplicity further underscores the advantages of switchracks. Pre-tested, pre-assembled racks arrive ready for immediate installation, significantly reducing the chance of costly installation errors and delays commonly experienced with substations.
Maintenance is similarly simplified, with standard practices clearly outlined and straightforward. Recommended procedures, such as periodic inspections, insulation resistance testing, protective device functional checks, and routine corrosion inspections, ensure operational reliability and safety with minimal downtime.
Conclusion: Making the Strategic Choice
Choosing between switchracks and substations hinges on multiple project-specific considerations, including cost, available space, safety requirements, and future flexibility. However, the strategic advantages offered by switchracks—particularly their substantial reductions in project timelines, costs, and complexity—position them as an optimal solution for many hazardous location installations.
As industry professionals, embracing switchrack technology means embracing efficiency, safety, and economic prudence. By understanding and advocating for this approach, engineers and EPCs can significantly enhance project outcomes, ensure compliance, and deliver lasting value to their organizations and clients.