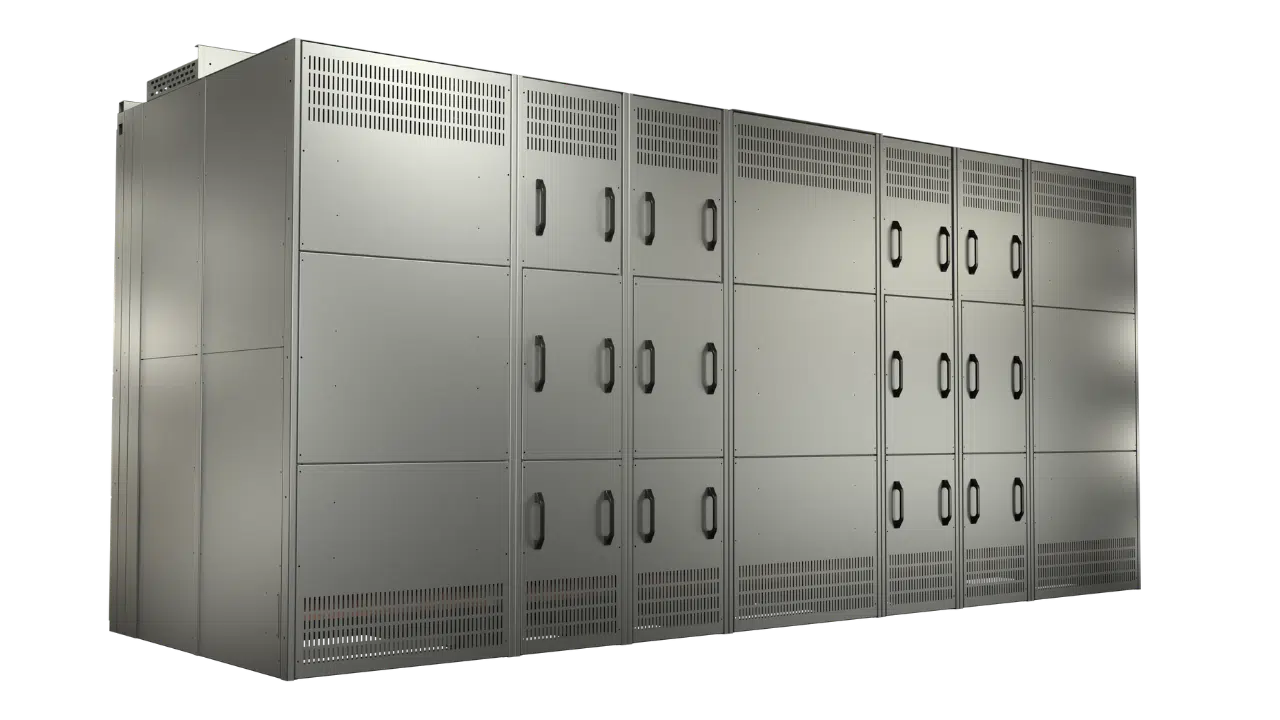
If you’re in the electrical industry, you’ve probably heard the terms UL 1558 Low Voltage Switchgear, IEEE C37.20.1 Metal-Enclosed Switchgear, or Low Voltage Power Circuit Breaker Switchgear. But what do these terms actually mean, and why do they matter? Whether you’re an engineer, contractor, or facility manager, understanding low voltage switchgear is critical to making informed decisions about power distribution, safety, and compliance.
What Is Low Voltage Switchgear?
At its core, low voltage switchgear is an assembly of electrical components designed to control, protect, and distribute electrical power at voltages up to 1000V AC. It houses essential devices like:
- Power circuit breakers – Used for system protection and fault isolation.
- Busbars – Conductors that distribute electrical power within the assembly.
- Protective relays – Devices that detect electrical faults and trigger circuit breakers.
- Instrument transformers – Used for metering and protection.
- Control panels and auxiliary devices – For remote operation, monitoring, and automation.
Think of low voltage switchgear like comparing an F-150 to an F-350 truck. Both are built to handle loads, but an F-150 switchboard is suited for lighter commercial applications, while an F-350 switchgear system is designed for heavy-duty power distribution and industrial-scale loads. The F-350 (switchgear) is built to handle higher fault currents, provide superior protection, and offer enhanced scalability, whereas the F-150 (switchboard) is perfect for smaller, less demanding environments.
Why Low Voltage Switchgear Matters
If you’re working with industrial power systems, commercial buildings, or utility substations, low voltage switchgear is at the heart of your electrical infrastructure. It ensures that power is distributed efficiently and safely while preventing catastrophic failures that could damage equipment or even put lives at risk.
Here’s why it’s so important:
- Protection Against Faults – Switchgear isolates faults, preventing cascading failures in electrical networks.
- Operational Safety – Protects workers from electrical hazards by providing a controlled, enclosed system.
- Compliance with Regulations – UL 1558 and IEEE C37.20.1 set the standards for performance and safety.
- Scalability – Modular designs allow for expansion as power needs grow.
UL 1558 vs. IEEE C37.20.1: What’s the Difference?
Many people confuse UL 1558 and IEEE C37.20.1, thinking they’re interchangeable. They’re not. While they both apply to low voltage switchgear, they serve different roles:
- UL 1558: This is a product safety standard that manufacturers must comply with to ensure their switchgear meets rigorous safety and performance benchmarks. If it’s UL 1558 listed, you know it’s been tested to industry standards.
- IEEE C37.20.1: This is an engineering design and performance standard that defines the construction, testing, and application of metal-enclosed low voltage switchgear.
In other words, UL 1558 ensures the switchgear is safe, while IEEE C37.20.1 ensures it is designed and built to handle real-world electrical conditions.
Key Features of UL 1558 Low Voltage Switchgear
If you’re specifying or purchasing low voltage switchgear, here’s what you need to look for:
- High Short-Circuit Withstand Ratings – The switchgear must be able to handle short-circuit conditions without failure.
- Compartmentalized Design – Ensures separation between busbars, breakers, and control systems for safety and easier maintenance.
- Arc Flash Mitigation – Advanced designs reduce the risks of arc flash incidents, a major safety concern in the industry.
- Robust Construction – UL 1558 switchgear is built to withstand harsh environments, including industrial and utility applications.
This is just the beginning of what makes low voltage switchgear critical in today’s electrical industry. In the next sections, we’ll dive deeper into its applications, testing procedures, and why choosing the right manufacturer matters.
A Deep Dive into Low Voltage Switchgear: Technical Aspects You Need to Know
In our last discussion, we covered the fundamentals of low voltage switchgear, its purpose, and why UL 1558 and IEEE C37.20.1 compliance are critical. Now, let’s take a deeper dive into the technical design elements that make switchgear not just functional, but safe, reliable, and adaptable to industrial applications.
This blog will explore key insulation properties, busbar configurations, protection barriers, and operational mechanisms, pulling from the IEEE C37.20.1 Standard to provide a clear understanding of how these elements contribute to system integrity.
1. Insulation and Dielectric Strength in Low Voltage Switchgear
One of the most critical components of switchgear design is its insulation system. The insulation of primary conductors must withstand dielectric stress while also meeting flame resistance requirements.
A. Insulating Material Standards
- Dielectric Testing: All insulation materials used for conductor supports must pass dielectric withstand tests to ensure they can operate under high electrical stress without breakdown.
- Flame Resistance: The materials must comply with IEEE flame resistance tests, ensuring they do not contribute to fire hazards inside the switchgear enclosure.
- Class 105 or Higher Insulation: The busbars and connections must be supported by insulation materials that meet at least Class 105 temperature ratings, ensuring long-term stability even under high thermal loads.
This insulation design is critical for ensuring switchgear reliability, minimizing arcing risks, and maintaining the overall system’s safety standards.
2. Busbar Configuration and Connections
Busbars are the backbone of power distribution inside low voltage switchgear, responsible for efficiently conducting current between components. IEEE C37.20.1 outlines strict construction requirements to ensure safety and reliability.
A. Bare vs. Insulated Busbars
- Bare Busbars: While the standard allows for bare busbars, additional insulation is required in areas where clearance might be too close.
- Encapsulated Insulated Busbars: Some manufacturers opt for fully insulated busbars to provide extra protection against short circuits.
- Dielectric Strength Testing: All busbar designs must be tested to meet short-circuit withstand standards, ensuring they can handle large fault currents without damage.
B. Sectionalizing and Isolation
- Barrier Requirements: If busbars are divided into separate sections, physical barriers must be installed to segregate different bus sections.
- Access Points: The switchgear design must allow for safe access to the bus compartments while preventing accidental contact with live conductors.
These design considerations prevent phase-to-phase faults, improve heat dissipation, and ensure that switchgear compartments remain operational even during maintenance activities.
3. Protection Barriers and Circuit Breaker Compartmentalization
Protection barriers play a major role in compartmentalizing switchgear to enhance safety and prevent damage from circuit breaker operation.
A. Circuit Breaker Isolation
- Each power circuit breaker must be mounted in its own metal-enclosed compartment, reducing risks of gas or arc faults spreading between compartments.
- Ventilation Openings: These must be designed so that gases generated by a circuit breaker do not interfere with adjacent compartments.
- Interlocks for Safety: Mechanical interlocks must be installed to prevent operators from accessing fuse compartments when a breaker is live.
B. Access Doors and Covers
- Hinged Front Doors: Every switchgear structure must have a front door covering the circuit breaker compartment.
- Removable Top and Back Covers: For bus access, removable plates must be provided, but their size is limited to 1.12m² or 27 kg unless equipped with lifting assistance.
- Mechanical Latches: Designed to prevent accidental exposure to live electrical components while maintaining easy access for authorized personnel.
These construction features ensure operator safety and system integrity, while also making switchgear easier to maintain and inspect.
4. Operational Mechanisms: Closing and Tripping Functions
Reliable switchgear operation requires precisely engineered mechanical systems for closing and tripping circuit breakers.
A. Manual and Electrical Operation
- Manual Tripping: Breakers must be equipped with manual trip buttons that allow operators to deactivate a breaker without exposure to live parts.
- Electric Operation: Electrically controlled breakers must allow for remote tripping but are not required to have manual closing functions, per IEEE guidelines.
These mechanisms ensure rapid fault isolation and reliable operational control, keeping power systems stable and safe.
5. Indoor vs. Outdoor Switchgear Requirements
Low voltage switchgear must be designed to withstand environmental conditions based on whether it’s installed indoors or outdoors.
A. Indoor Switchgear
- Must be built with ventilated enclosures to allow for heat dissipation.
- Primary function is to protect equipment from accidental contact, rather than extreme weather.
- Typically found in industrial plants, commercial buildings, and data centers.
B. Outdoor Switchgear
- Requires sealed, weatherproof enclosures to prevent moisture ingress.
- Must be designed to withstand temperature fluctuations, UV exposure, and environmental contaminants.
- Often used in utility substations, power distribution yards, and industrial outdoor facilities.
By meeting IEEE C37.20.1 standards for environmental protection, switchgear manufacturers ensure that power distribution remains stable, safe, and long-lasting regardless of installation location. Understanding the technical aspects of low voltage switchgear is essential for engineers, facility managers, and contractors who need to design, specify, or maintain electrical distribution systems. From insulation properties to busbar configurations, each component plays a vital role in ensuring system safety, reliability, and compliance with industry standards.
By following IEEE C37.20.1 guidelines, manufacturers and operators can ensure that their switchgear meets modern electrical performance and safety demands, helping to prevent faults, enhance efficiency, and improve long-term system reliability.
Optimizing Low Voltage Switchgear: Advanced Design and Performance Considerations
Following our previous deep dive into low voltage switchgear design, this blog builds on that foundation by exploring additional critical aspects of grounding systems, ventilation, short-circuit withstand capabilities, and seismic ratings. These elements are essential to ensure the reliability, efficiency, and safety of switchgear systems in both standard and extreme conditions.
1. Grounding Systems: Ensuring Safety and Fault Protection
Proper grounding in low voltage switchgear is critical for fault protection, operator safety, and system stability. The grounding system must be designed to effectively carry fault currents and minimize electrical hazards.
A. Grounding Conductors and Methods
- Main Ground Bus (MGB): A dedicated copper or aluminum ground bus must be installed, connecting all metal components of the switchgear assembly.
- Equipment Bonding: All metallic enclosures, frames, and non-current-carrying metal parts must be bonded together to prevent potential differences.
- Neutral-to-Ground Bonding: Where required, a neutral-to-ground bond is used in main switchgear assemblies to provide a direct path for fault current return.
B. Ground Fault Protection
- Sensitive Ground Fault Relays: These are installed to detect leakage currents and isolate faults before damage occurs.
- Low-Impedance Grounding: Helps reduce fault currents and prevents high transient voltages that could damage equipment.
- Testing and Verification: Ground resistance testing ensures compliance with IEEE and NEC grounding standards.
2. Ventilation and Cooling: Managing Heat Dissipation
Low voltage switchgear generates heat during normal operation, and proper ventilation and cooling are essential for maintaining system longevity and preventing failures.
A. Heat Dissipation Strategies
- Passive Ventilation: Natural airflow through vented enclosures helps dissipate heat from busbars and circuit breakers.
- Forced Air Cooling: Some designs use integrated fan systems to improve airflow and keep components within safe operating temperatures.
- Heat Sinks and Radiators: In higher current applications, switchgear assemblies may include additional cooling elements to enhance heat dissipation.
B. Enclosure Design for Thermal Management
- Airflow Pathways: Switchgear must be designed with adequate clearance for air circulation, preventing thermal buildup.
- Sealed Enclosures for Outdoor Use: Outdoor switchgear requires special consideration for moisture resistance while maintaining effective ventilation.
- Temperature Sensors: Integrated sensors monitor operating temperatures and trigger alarms if thresholds are exceeded.
3. Short-Circuit Withstand Capabilities: Strength Under Fault Conditions
The ability of low voltage switchgear to withstand and clear short-circuit faults is one of the most important performance characteristics.
A. Short-Circuit Ratings
- Withstand Ratings (WCR): Defines the maximum short-circuit current the switchgear can endure without sustaining damage.
- Interrupting Ratings: The circuit breaker’s ability to open and clear fault currents safely, measured in kiloamperes (kA).
- Coordination Studies: Engineers perform fault current studies to ensure that switchgear ratings match expected short-circuit conditions in the system.
B. Reinforcement for Fault Resilience
- Bracing for Busbars: Busbars are mechanically braced to withstand short-circuit forces without excessive movement.
- Arc-Resistant Design: Some switchgear enclosures include reinforced materials and exhaust pathways to minimize the impact of internal arc faults.
- Advanced Protection Relays: High-speed relays ensure that breakers trip quickly in response to fault conditions.
4. Seismic Ratings: Designing for Earthquake Resistance
For installations in seismic-prone areas, switchgear must comply with seismic ratings to ensure continued operation and safety during an earthquake.
A. Structural Reinforcements
- Seismic Bracing: Reinforced frame structures and base anchors prevent excessive movement during seismic activity.
- Shock-Absorbing Mounts: Some switchgear assemblies include vibration-dampening elements to reduce stress on components.
- Seismic Testing Compliance: Certified switchgear is tested to meet IEEE 693 seismic standards for high-risk earthquake zones.
B. Flexible Connections and Cable Management
- Flexible Busbar Connectors: Allow movement without stressing electrical joints.
- Secured Cable Routing: Ensures that conductors remain intact and operational during ground shifts.
- Post-Seismic Inspection Protocols: After seismic events, operators must perform thorough inspections before re-energizing the switchgear.
Comprehensive Testing and Maintenance for Low Voltage Switchgear
Continuing our previous discussions on low voltage switchgear design and performance, this section explores the critical testing and maintenance procedures necessary to ensure long-term operational integrity and compliance with industry standards. Proper maintenance and periodic testing are essential for preventing failures, improving safety, and extending the lifespan of switchgear assemblies.
1. Pre-Operation Checks and Initial Testing
Before energizing a newly installed low voltage switchgear system, a series of pre-operation checks must be conducted to ensure all components are functioning as intended.
A. Mechanical and Electrical Inspections
- Tightening of Connections: All bolted connections and joints should be inspected and torqued to manufacturer-recommended values.
- Verification of Internal Components: Checking for damage, foreign objects, or loose wiring that may have occurred during shipping or installation.
- Manual Circuit Breaker Operation: Each breaker must be manually operated using closing levers and trip mechanisms to confirm functionality.
B. Control Wiring and Insulation Resistance Testing
- Continuity Tests: Control wiring should be verified for proper routing and connectivity.
- Insulation Resistance Testing: A 500V insulation resistance tester should be used to ensure no unexpected leakage paths exist in control circuits.
- Phase Rotation and Sequence Checks: Ensuring correct phase alignment before energization to prevent operational issues.
These pre-operation checks are crucial for identifying potential failures before they result in costly downtime or system malfunctions.
2. Field Testing and Dielectric Withstand Tests
Once pre-operation checks are complete, field dielectric tests should be conducted to verify insulation integrity and compliance with IEEE C37.20.1 standards.
A. Dielectric Testing Protocols
- Power Frequency Withstand Tests: Applied at 75% of factory test values to verify the system’s ability to handle operating voltages safely.
- DC Withstand Tests (For DC Switchgear): Ensuring bus insulation can support expected voltage levels without breakdown.
- Test Environment: Tests should only be conducted in a clean and dry setting to prevent false insulation failures.
These tests help confirm that the switchgear has not been compromised during transportation, installation, or long-term service.
3. Circuit Breaker Testing and Interlock Verification
Circuit breakers are one of the most critical components in low voltage switchgear. Regular testing ensures they function properly under normal and fault conditions.
A. Circuit Breaker Inspection and Operation
- Manual and Electrical Closing Tests: Each breaker should be tested manually and through control circuits to confirm reliable operation.
- Trip Mechanism Testing: Manually activating the trip function ensures the breaker disengages under fault conditions.
- Voltage Range Testing: Breakers must be tested at normal and minimum control voltage levels as defined in IEEE Std C37.13 and C37.14.
B. Interlock System Validation
- Prevention of Live Removal: Interlocks must be tested to ensure breakers cannot be moved from the connected position while closed.
- Position-Based Closing Protection: The circuit breaker should not close unless fully connected or in the designated test position.
- Key Integrity and Security: Duplicate interlock keys should be destroyed or secured to prevent unauthorized access.
Regular circuit breaker and interlock testing prevents mechanical failures, ensuring the safety of both personnel and equipment.
4. Maintenance Procedures for Long-Term Reliability
Routine maintenance helps prevent failures and prolongs the lifespan of low voltage switchgear. The following tasks should be scheduled at regular intervals.
A. Routine Preventive Maintenance
- Visual Inspections: Periodic checks for signs of overheating, corrosion, or physical damage.
- Cleaning and Lubrication: Removing dust buildup and applying approved lubricants to moving parts.
- Busbar and Connection Integrity Checks: Ensuring proper alignment and torque settings for power connections.
B. Thermographic and Partial Discharge Testing
- Infrared Thermography: Detects hot spots in busbars, connections, and breakers before failure occurs.
- Partial Discharge Analysis: Identifies insulation degradation and corona discharge effects in high-stress areas.
- Ultrasonic Testing for Arcing: Helps detect internal faults that could lead to insulation breakdown or component failure.
By combining visual inspections, infrared analysis, and electrical testing, switchgear reliability can be maintained with minimal unplanned downtime.
5. Energization and System Commissioning
Once all testing and maintenance checks are complete, the switchgear system is ready for energization and commissioning.
A. Final Pre-Energization Steps
- Final Control Scheme Testing: Ensuring all operational sequences are functioning correctly.
- Breaker Position Lock-In: Confirming all breakers are in their correct operational state before applying power.
- Protective Relay Coordination: Verifying protective devices are correctly set based on the facility’s power distribution study.
B. Safe System Energization
- Gradual Power Application: Bringing the system online in stages to monitor for unexpected behavior.
- Monitoring Initial Load Conditions: Checking voltage, current, and phase balance to ensure stability.
- Operator Training and Handover: Providing on-site personnel with guidance on proper switchgear operation and emergency procedures.
Comprehensive testing and scheduled maintenance are essential for ensuring low voltage switchgear remains reliable, compliant, and safe throughout its operational life. From pre-installation checks to field testing and long-term maintenance, each step plays a crucial role in preventing failures and optimizing performance.
By following IEEE and UL standards for dielectric testing, circuit breaker validation, and insulation resistance monitoring, operators can minimize downtime, enhance safety, and extend the lifespan of their electrical infrastructure.
Stay tuned for our next blog, where we’ll explore protective relay coordination and fault mitigation strategies for advanced switchgear applications!
Advanced Protection and Isolation Strategies for Low Voltage Switchgear
Continuing from our previous discussions on switchgear testing and maintenance, this article focuses on advanced protection, isolation methods, and special applications for low voltage switchgear. Understanding these concepts ensures compliance with IEEE C37.20.1 standards and optimizes system performance for demanding environments.
1. Voltage Circuit Protection: Ensuring Stability and Fault Prevention
Voltage circuits used for control, relaying, and metering within switchgear must be protected according to IEEE and NEC regulations. These protections prevent faults and ensure system integrity.
A. General Protection Requirements
- External Supply Protection: Circuits sourced externally must have short-circuit protection at the incoming section.
- Internal Supply Protection: Internally supplied circuits must have short-circuit protection within the same vertical section as the power source.
- Overcurrent Protection Compliance: Must adhere to NFPA 70 (NEC) unless circuit interruption creates operational hazards.
- Separate Bus Connections: Voltage circuits connected directly to the main bus must be grouped separately and minimized in length to reduce interference.
- Load Circuit Protection: Any circuits supplying heaters, receptacles, or lighting require overcurrent protection.
These protections ensure that voltage fluctuations, overloads, or unexpected faults do not compromise system reliability.
2. Control Power Transformers and Voltage Transformers: Safe Power Distribution
Control power transformers (CPTs) and voltage transformers (VTs) play a crucial role in switchgear operation, providing reliable voltage regulation and protection for critical circuits.
A. Short-Circuit Protection for Control Power Transformers
- Primary current-limiting fuses should be installed per NFPA 70 (NEC) Table 450.3(B).
- Fuse Sizing: Proper selection prevents excessive inrush currents while maintaining system safety.
- Isolation Measures: Dead-front design switches or fuse pullouts should be used when primary disconnects are necessary.
B. Voltage Transformer Protection
- Primary circuits require current-limiting fuses no larger than 10 A.
- Isolation Requirements: All devices connecting to primary circuits must be housed in dead-front enclosures to reduce electrical hazards.
Proper transformer protection ensures stable voltage regulation, prevents unnecessary tripping, and enhances electrical safety.
3. Current Transformer (CT) Secondary Protection and Relay Coordination
Current transformers (CTs) measure current flow and are essential for protection relay operation. Proper secondary circuit protection ensures CTs perform accurately without excessive burden or risk of failure.
A. Current Transformer Secondary Circuit Protection
- Overcurrent protection is generally avoided for CT secondary circuits.
- Open Circuit Protection Consideration: To prevent dangerous voltages, open circuit protection is applied where CTs connect to devices outside the switchgear assembly.
- Short-Time Rating Compliance: All protective devices must be coordinated with short-time ratings to ensure proper tripping and load isolation.
Relay coordination is essential for maintaining selective tripping, ensuring that the closest upstream protective device isolates a fault without unnecessary disruption to the entire system.
4. Isolation and Tie-Circuit Protection in Multi-Switchgear Systems
When multiple low voltage switchgear assemblies are connected, tie-circuit protection is required to prevent cascading failures in the event of a fault.
A. Isolation Between Multiple Switchgear Assemblies
- Protective Equipment for Tie Circuits: A properly rated tie circuit breaker or disconnect switch should be installed between connected switchgear.
- Selective Tripping Considerations: Upstream and downstream protective devices must be coordinated to ensure that a fault in one assembly does not cause the failure of another.
- Guidance from Industry Standards: Referencing IEEE Std 141, 142, and 242 provides best practices for isolation design in complex electrical systems.
Ensuring adequate tie protection allows multiple switchgear units to operate independently, reducing the risk of widespread power disruptions.
5. Overcurrent Protection and Grounding in Low Voltage Switchgear
Proper overcurrent protection and grounding schemes prevent damage due to excessive fault currents and enhance safety for personnel working near switchgear systems.
A. Overcurrent Protection Strategies
- AC systems require overcurrent protection for each ungrounded phase conductor.
- DC traction power systems operate with isolated grounding to reduce arc flash hazards.
- Arc Flash Hazard Reduction: Ungrounded or high-resistance grounding systems minimize risk exposure in transit applications.
B. Grounding Considerations
- LV AC Switchgear Grounding:
- Reconnect ground bus at shipping sections during installation.
- Ensure proper ground conductor sizing for line-to-ground fault duration.
- Establish a permanent low-resistance ground connection separate from other electrical systems.
- LV DC Switchgear Grounding:
- High-resistance grounding systems require dielectric testing before final connection.
- Ground/live relay monitoring detects abnormal voltage conditions.
- Shielded wiring should not introduce external grounds to isolated enclosures.
These practices ensure fault current containment, equipment longevity, and compliance with IEEE grounding recommendations.
Advanced voltage circuit protection, relay coordination, grounding, and isolation strategies are essential for maintaining a safe and efficient switchgear system. By ensuring proper protection for voltage circuits, transformers, and CTs, operators can reduce downtime, enhance system selectivity, and prevent widespread electrical faults.